The almond shelling production line could shell and peel almonds, and it includes two parts: almond shelling and separating plant, and almond peeling plant. The main machine used in this production line is the almond shelling machine, almond shell separator, and soaked almond peeling machine. The almonds produced by this line are clean and full-grained, and can be packaged into bags for sale or made into snacks. The capacity of this plant can be tailor-made.
Watch the Video of Almond shelling processing machines
Machine Application
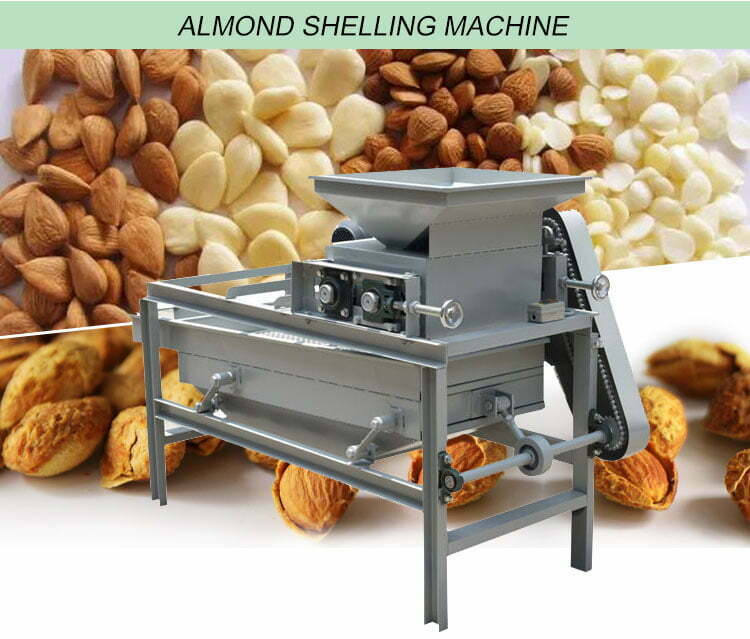
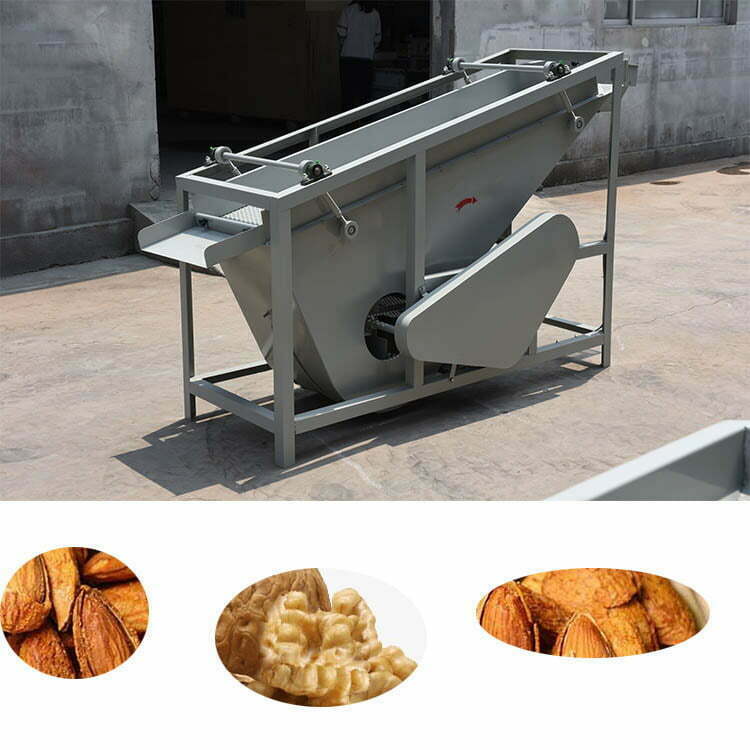
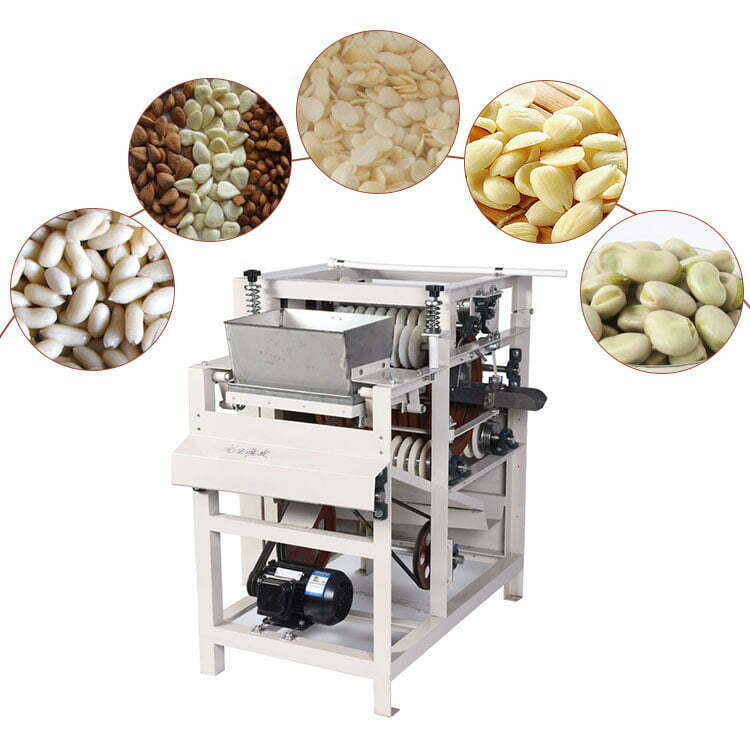
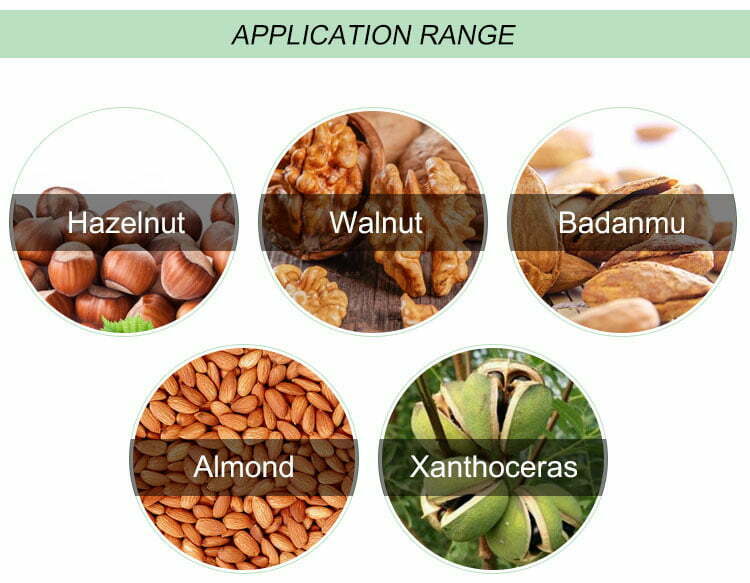
Almond Shelling and Separating Plant
The almond shelling production line includes: the feeding hopper, skip the elevator, almond classifying machine, apricot shelling machine, conveyor belt, elevator, almond shell, and kernel separator.
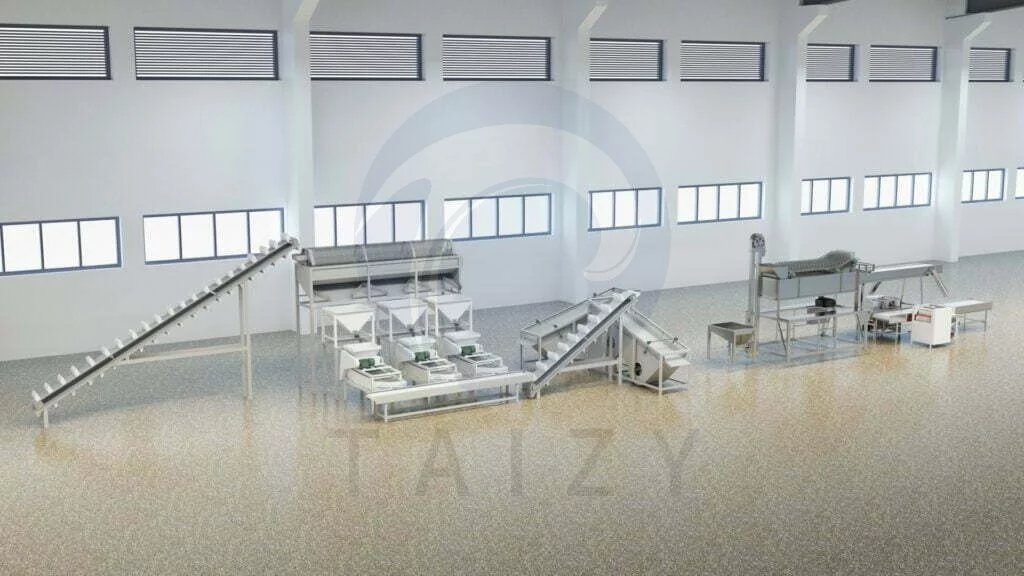
Almond skip elevator
- Size: 3.5m*0.6m*0.6m
- Power: 0.75kw
- carbon steel, PVC bucket belt
Workers pour raw materials into the feeding hopper, and this elevator will hoist materials into the grading machine and continue the next processing. It could save labor, and improve work efficiency.
Roller classifier machine
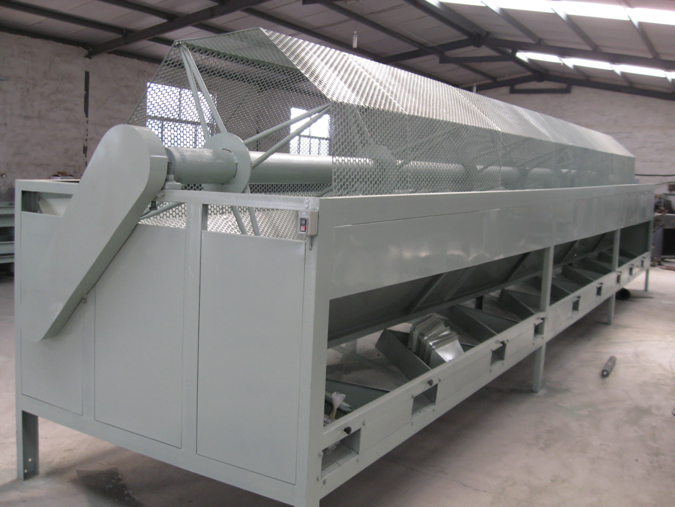
- Size: 2.4m*0.8m*1.4m
- Power: 1.1 kw
- Voltage: 380v
- Frequency: 50hz
- Output: 600-800kg/h
- Power: 1.1kw
- Voltage: 380v, 50hz
This classifying machine is mainly used to grade different sizes of apricot kernels, hazelnuts, almonds, different fruit beans, etc. It divides materials into three levels large, medium, and small for easy storage. The roller classifier has different sizes of holes and through continuous rolling, almonds of different grades will discharge into dividing hoppers. It improves the shelling effect.
Almond sheller machine
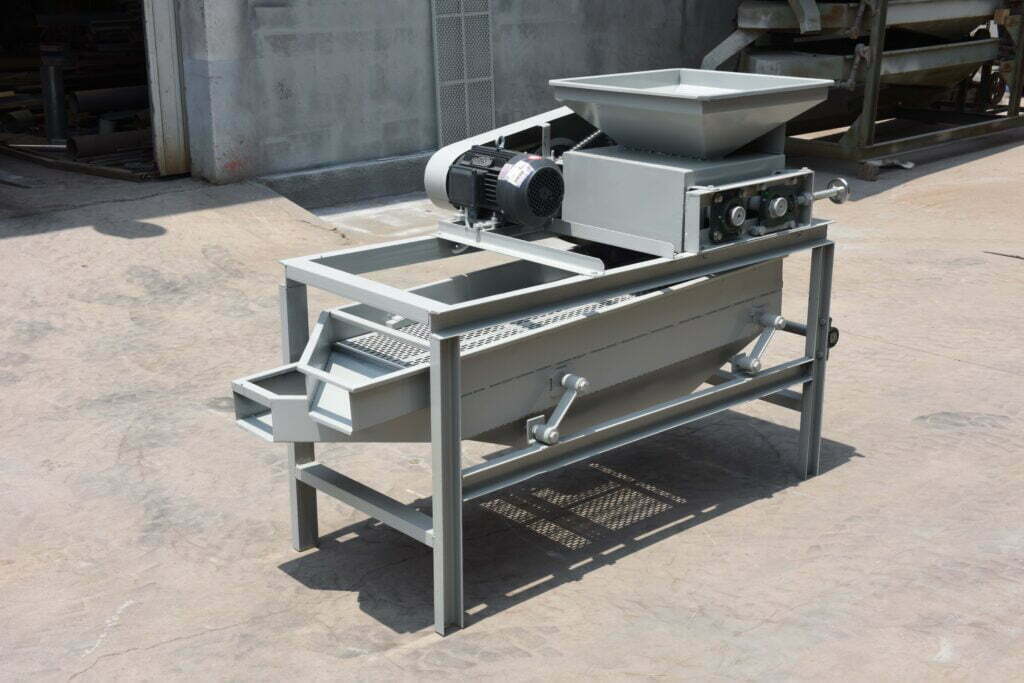
- Output: 300-400kg/h
- Power: 2.2kw
- Voltage: 380v
- Frequency: 50hz
- Size: 1.8m0.8m1.5m
- Weight: 240kg
This almond shelling machine is mainly used to crack the hard shells of various specifications of almonds in the almond shelling production line. It consists of processing dehulling rollers and a vibrating screen. This sheller could crack hard shells such as apricot kernels, hazelnuts, and jujubes at a time. And the gap between the processing rollers can be adjusted. The design is reasonable and the crushing rate is low, which is the most ideal nuclear processing equipment at present.
- The machine is a two-layer design. The first layer will separate the full-grained, larger almonds. The second layer is relatively small almonds. Residues are separated at the bottom of the equipment, and almonds of different sizes can be separated from each layer.
- There are handles on both sides of the machine for adjustment, which can peel off dried fruits of different specifications and diameters.
Conveyor belt
The shells and kernels of almonds will be discharged onto this belt and be conveyed to the hoist.
Elevator
This elevator hoists apricot shells and kernels onto the almond gravity separator machine.
Almond shell kernel separator
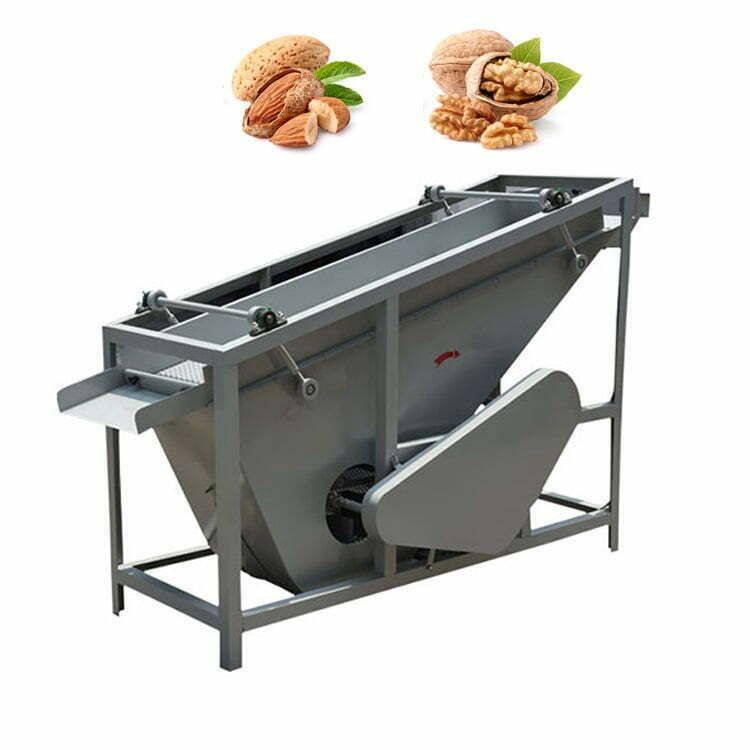
- Size: 2.4m0.8m1.6m
- Weight: 220kg
- Power: 2.2kg
- Voltage: 380v
- Frequency: 50kz
- Output: 300kg
This separator is mainly used to separate apricot kernels, hazelnut shells, walnuts, shells, and kernels in the almond shelling production line. The specific gravity and suspension speed of shells and kernels are used to separate the shells and kernels with the help of the airflow passing upward through the particle gap. Through the different proportions of almond shells and apricot kernels, this machine could reach the best separation effect. The separation rate of general varieties is 90-95%.
This machine is composed of a feeding hopper, screen body, fan and frame, eccentric transmission mechanism, and other parts. The joint of the reciprocating motion of this machine adopts rubber bearings, which are durable and shock-absorbing. This machine is used to control the size of the wind coming in and the angle of the shaking machine to get a good depart of the shell and the seeds.
Almond Peeling Production Line
Workflow: feeding hopper, elevator, soaking machine, conveyor belt, peeling machine, picking line.
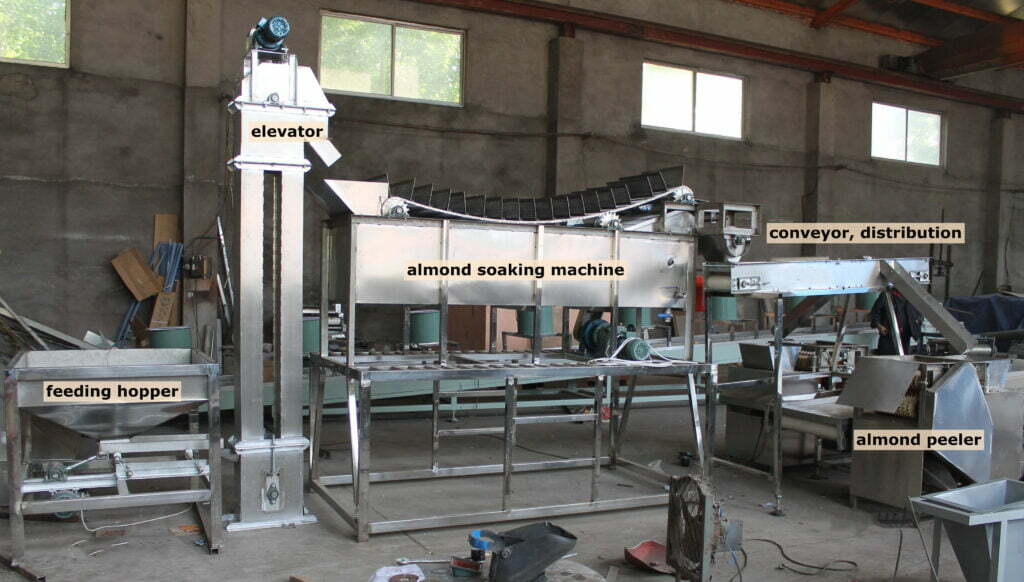
Elevator
This elevator could lift the shelled almonds into the soaking machine. And before this elevator, there is a feeding hopper.
Almond soaking machine
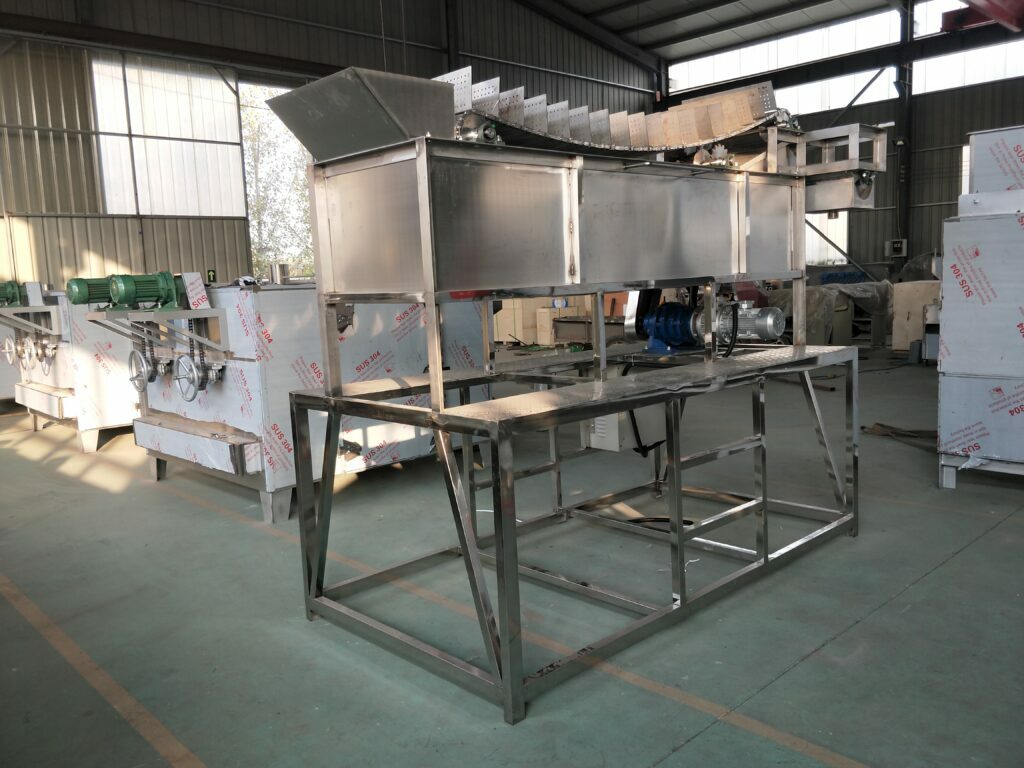
For this is a wet almond peeling plant, before the almond peeling machine, a soaking machine is designed to wet the almonds.
Generally, soak for 5-10 minutes, the water temperature is about 100℃.
Conveyor belt (almond distribution)
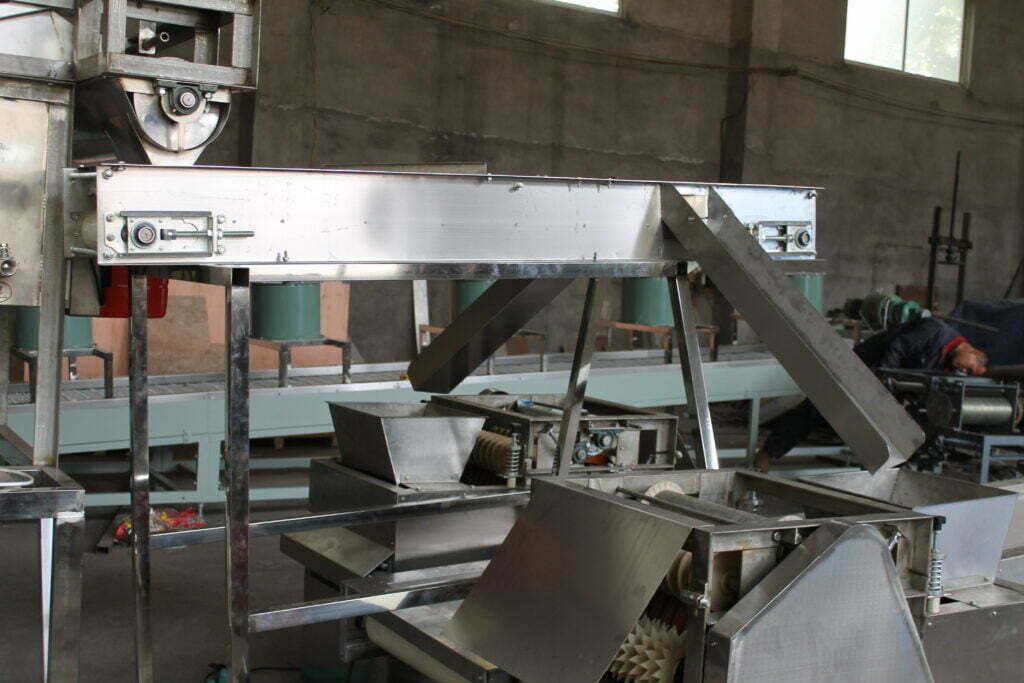
Wet almonds are discharged into this conveyor. And it distributes materials to the almond peeling machines.
Soaked almond peeling machine
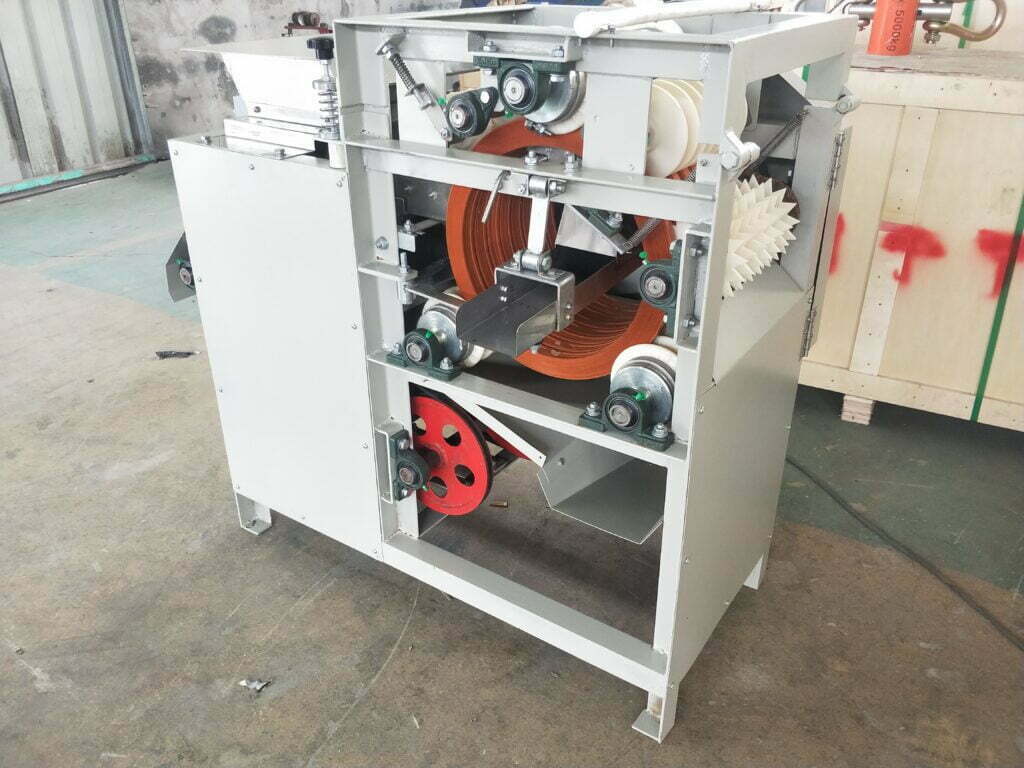
- Size: 1.15m*0.85m*1.1m
- Power: 0.75kw
A wet almond peeling machine is professional equipment for peeling peanuts, almonds, soybeans, and other beans. It is widely used in the production of fried peanuts, broad beans, almond milk, flavored peanuts, peanut cakes, peanut candy, peanut milk, peanut eggs, eight-treasure porridge, peanut butter, canned food, and other products. The unique feature of this machine is its high peeling rate. The peeled peanuts, almonds, soybeans, and broad beans are not broken. The color is white and the protein does not change. While peeling, the skin and rice are automatically separated. In addition, the machine has the characteristics of small size, low energy consumption, high efficiency, and easy operation.
- Add the soaked peanuts to the hopper of the machine.
- Almonds enter the peeling rubber wheel through the feed screen.
- It removes the skin while rotating, and separates the skin and kernel at the same time.
Picking belt
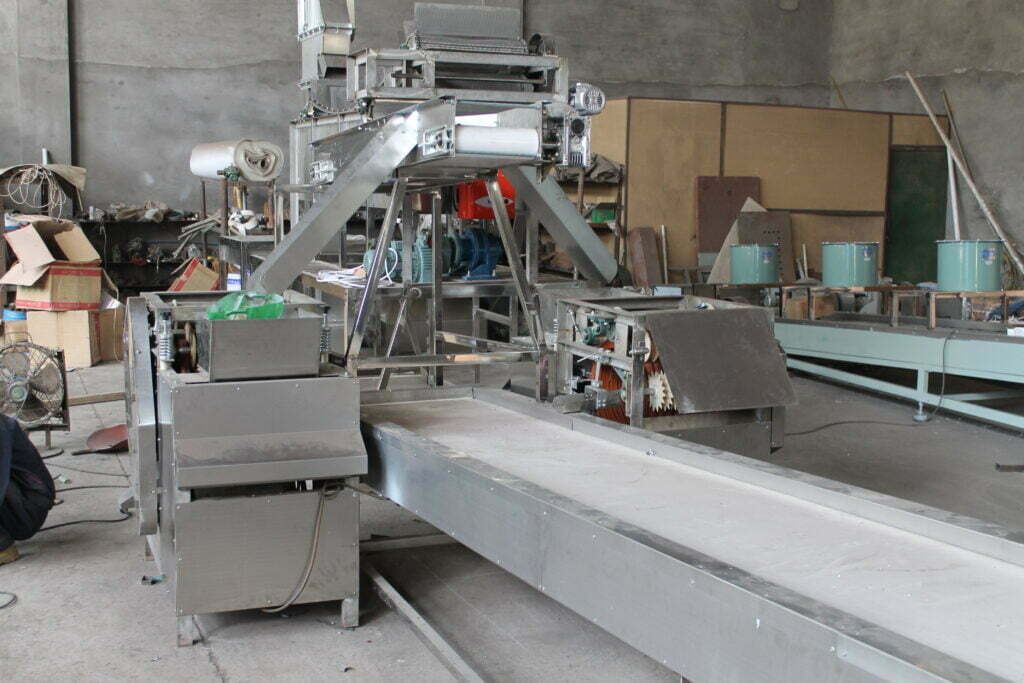
Peeled almonds will output onto this belt and workers could pick out those unpeeled almonds.
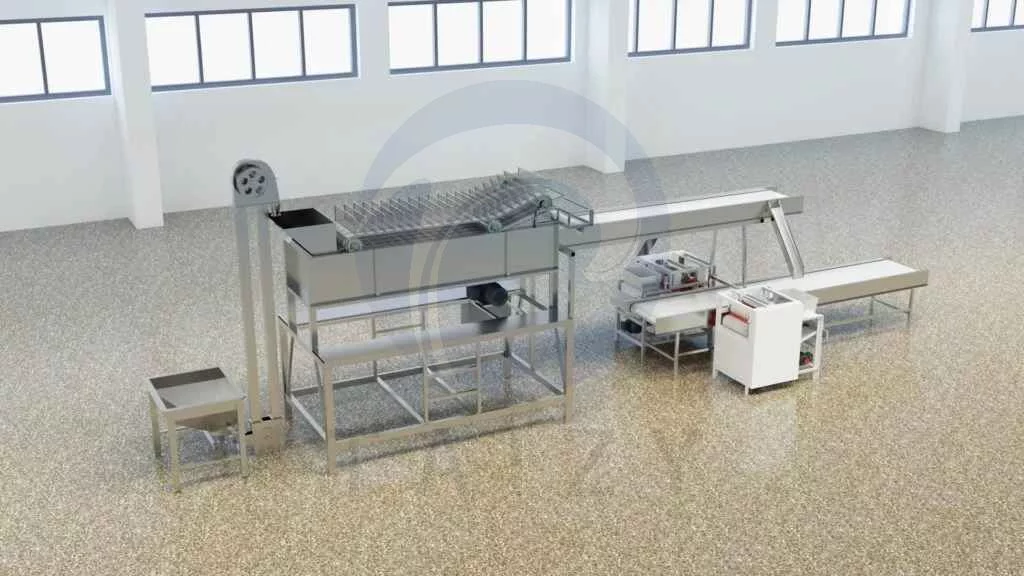
Highlights of almond shelling production line
- Multiple Capacity
We provide 400kg/h, 500kg/h, and 1000kg/h almond shelling production line. Customers could also make a specific output according to their needs.
- High Shelling Effect
The equipment runs smoothly, with low noise, large output, factory direct sales, and quality guaranteed.
- Healthy Work
The almond sheller adopts a purely physical shelling method, which is energy-saving and environmentally friendly, guarantees food safety, and improves production efficiency.
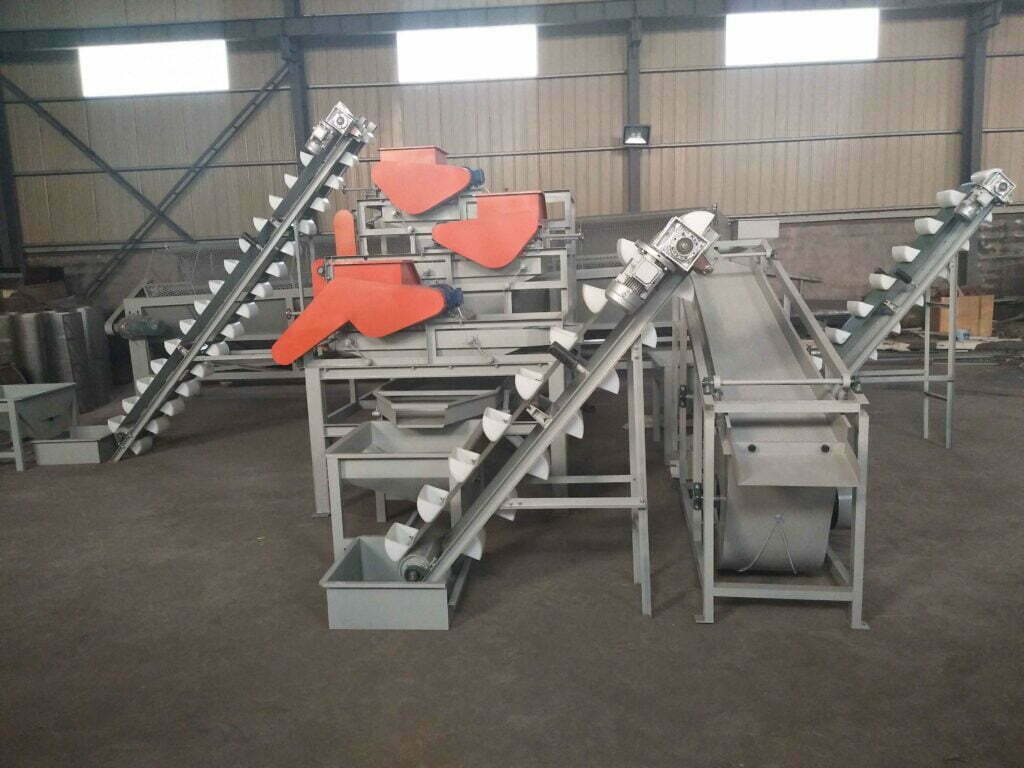
Maintainance of apricot kernel peeling machine
- There are more kernels in the peeled skin.
The discharge wheel is too high and the distance between the leather shaft is too large.
Lower the discharge wheel so that it is attached to the squeezing shaft.
- There is more skin in the peeled almonds.
The discharge wheel is too low, causing the squeezing shaft to leave the inner ring of the rubber wheel.
Raise the discharging wheel so that the extruding shaft keeps good contact with the rubber and discharging wheels.
The sling wheel does not turn or is damaged.
Adjust and replace the slinging wheel.
After the chain is installed, the direction of rotation of the sling wheel is wrong.
Reinstall the chain.
- There are many unpeeled kernels flowing out of the hopper.
The induction strip is broken or the curvature of the induction strip does not match the rubber wheel.
Replace or adjust.
Uneven size of raw materials.
Classify raw materials.
The baffle plates on both sides of the feed screen in contact with the rubber wheel are too short.
Replace the baffle plate.
- The rate of two petals or broken rate of kernels after peeling is higher.
The gap of the rubber wheel is too small.
Increase rubber wheel gap.
The soaking time of the raw materials exceeds the process requirements. That is, the time is too long.
Strict process, soak in the specified time.